In previous posts I evaluated and selected a tensioner, I had a custom GripTec supercharger pulley machined and I had a massive 9.7” Superdamper machined. Today I finally completed the rest of supercharger’s serpentine system. It was a lot of work. There are no OEM parts, most of the aftermarket parts are custom and I designed and fabricated everything else.
The large plates were laser-cut from 1/4” 304 stainless steel (prior pictures were of the mild-steel prototypes). I used a horizontal belt sander to clean up the outer edges and a Dremel loaded with a small sanding drum for the circular cutouts and a few of the tight radiuses that the belt sander couldn’t reach. To break the edges I used a deburring tool on the interior features and a deburring wheel on the exterior. The result isn’t as nice as CNC’d pieces, but it’s close at a fraction of the price.
Since the cylinders are staggered the right head (left side of picture) sits behind the plane of the block and the left head. I machined four aluminum spacers to sit between the head and the rear plate, but it was unwieldy to hold them in place when installing the brackets so I had Abe weld them to a frame.
The right head (left side of the picture) sits behind the front of the block and left head
Spring/Roll/Tension/Split/Expansion Pin
The shape of the spacer for the tensioner wouldn’t of been trivial to mill and the holes needed to be precise so I decided to have it laser cut. However, the spacer was thicker than the laser could handle so I cut two pieces and milled one of them to meet the target thickness. I then used two spring pins (aka roll, tension, split, or expansion pins) to prevent them from moving in relation to one another. Spring pins have a slot in them and when they are hammered into an undersized hole they spring outwards and apply tension. I have used them in steel parts before, but I found that they gouged the side of the aluminum holes and pushed material into the hole. To address, I tried to compress the beveled end with pliers which resulted in the pin being shot across the room. I found that a vice allowed me to get the perfect amount of compression without the launching problem. This allowed me to pound the pins in. They would be a bitch to remove which is exactly what I wanted for this application because they will never be removed. The final step was to clean up the edges on a belt sander. If you look carefully at the picture below, you’ll see line separating the top and bottom pieces.
Two-piece spacer for the tensioner; top piece was machined to target thickness; both are pinned together
All of the other spacers were machined from 6061 rod on the lathe. Most were simple cylinders, but several required tight-tolerance shoulders to index the ID of the pulley bearings.
Two spacers and one cover with shoulders that index the ID of a pulley bearing
As mentioned in a previous post, I was able to get a Gates 10-rib MICRO-V FleetRunner (aka green belt) to fit. They have superior construction and are, to my knowledge, the best serpentine belts for supercharged applications. Beyond having superior construction, it is several inches shorter and 25% wider (i.e., 8 vs. 6 ribs) than the one provided by Harrop. Since elongation is proportional to length and inversely proportional to width, the belt will stretch less on first principals.
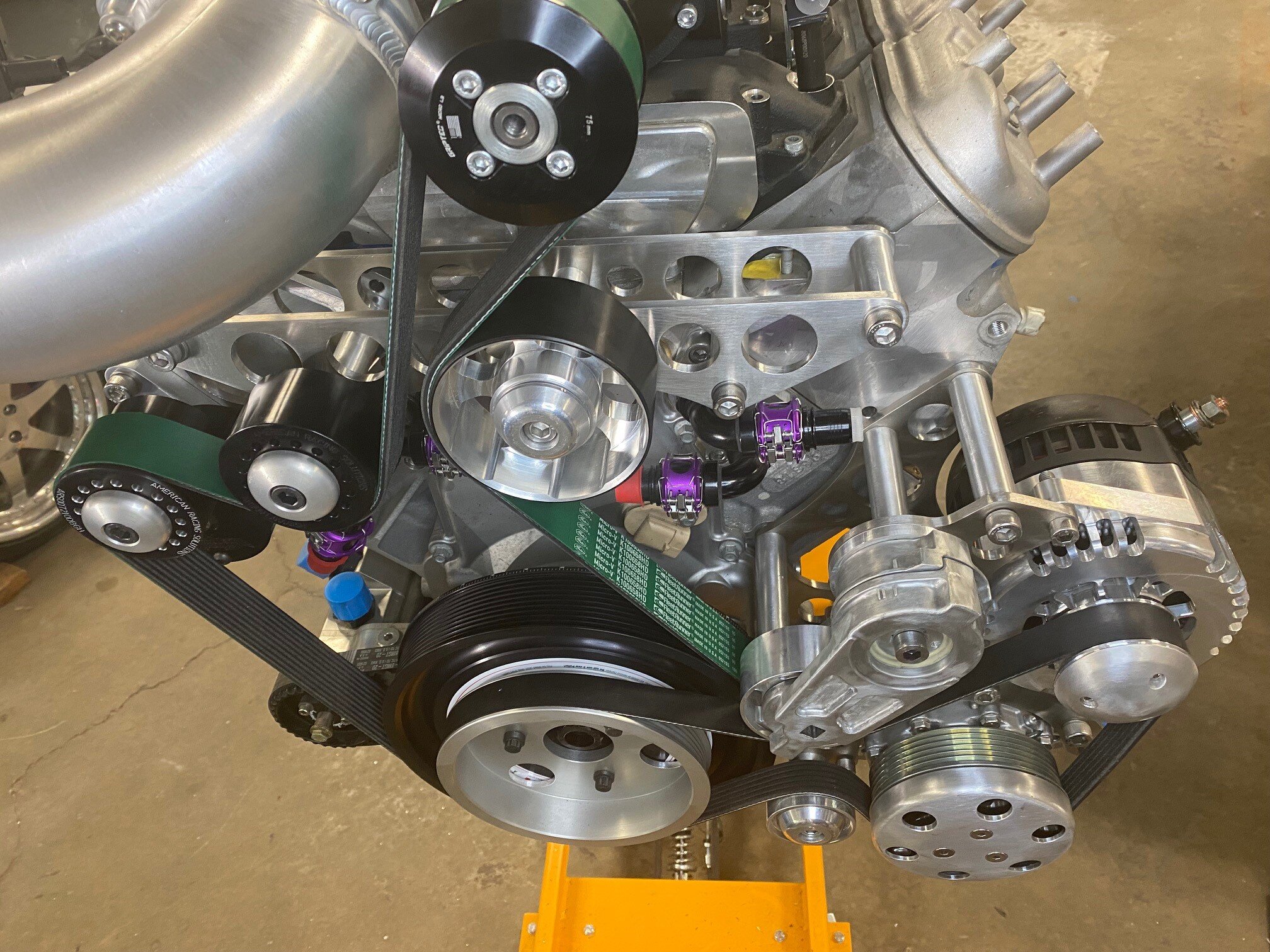
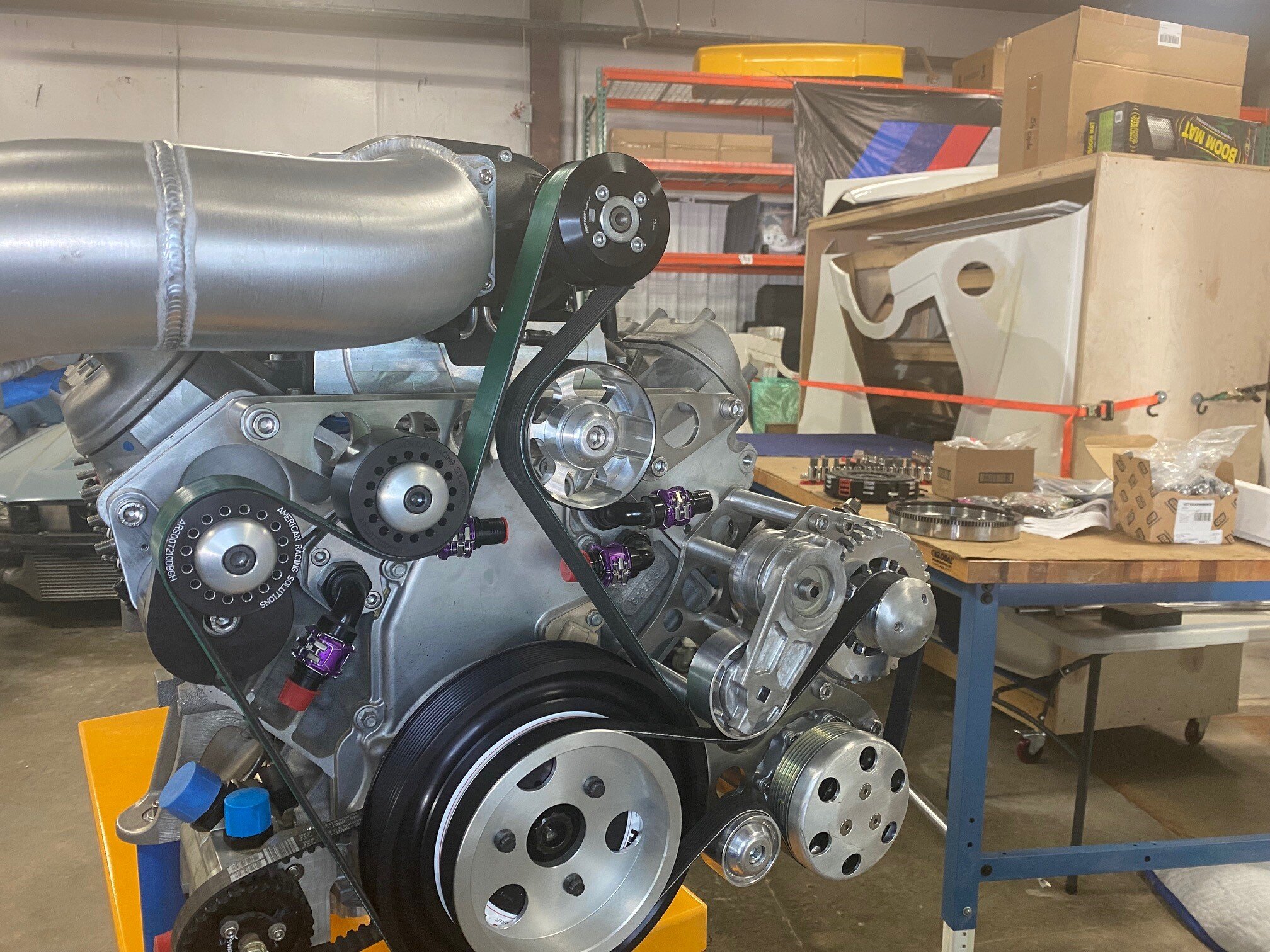

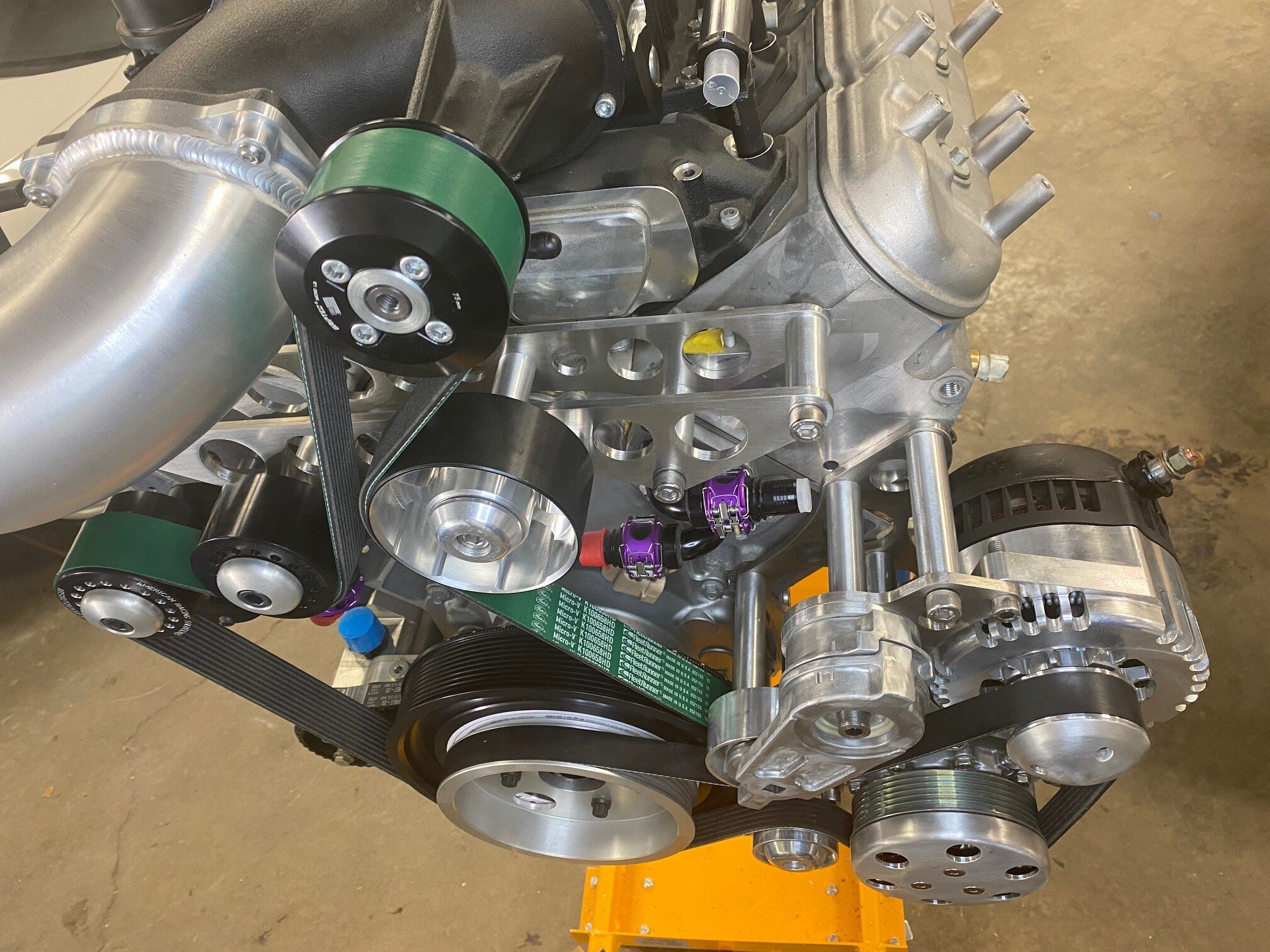